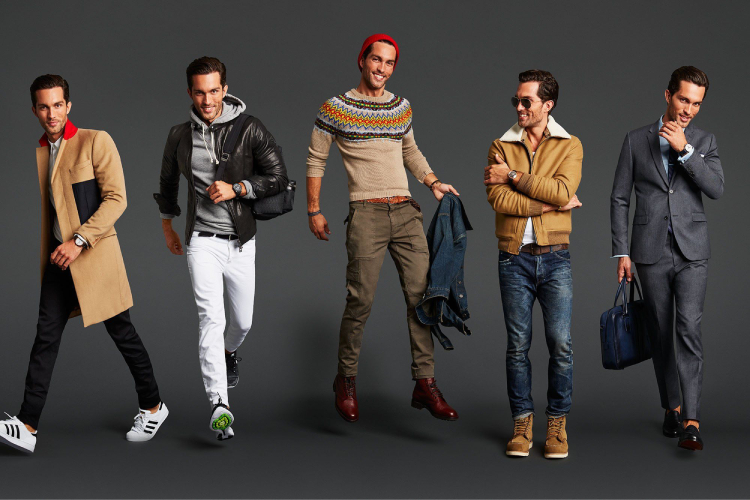
دنیم پارچه پنبه ای مستحکم و با دوامی است که در آن نخ پود از زیر دو یا تعداد بیشتری نخ تار می گذرد. پارچه های دنیم با نمره نخ بالا، چگالی بالا و طرح بافت 3 به 1 بافته می شوند. از دنیم بطور ویژه برای تولید جین ها (jeans) استفاده می شود و در البسه های دیگر نیز کاربرد دارد. شاید جین یکی از مهمترین مقوله های دنیای مد امروز باشد. دنیم بطور سنتی با رنگهای ایندیگو رنگرزی می شد تا "جین آبی" را بسازد. دنیم یک نماد و یکی از مهمترین محصولات شناخته شدهی صنعت نساجی است که همه گروه های سنی را به خود جذب می کند. در این مقاله توصیف جامعی در مورد تولید دنیم به کمک فلوچارت انجام شده است.
فلوچارت تولید پارچه دنیم:
ریسندگی
↓
چله پیچی
↓
رنگرزی طنابی
↓
باز کردن نخ های رنگرزی شده طنابی و پیچیدن آنها بر روی نورد جهت انتقال نوبتی بهواحد اجرای پروسه آهارزنی
↓
آهارزنی
↓
بافندگی
↓
تکمیل
↓
بررسی و تا کردن
↓
بسته بندی
↓
ارسال
تولید پارچه دنیم: (Manufacturing of Denim:)
واژه "دنیم" از شهری در فرانسه به نام " serge de Nimes " نشأت گرفته که در آنجا تولید می شد. دنیم از رنگ خمی(vat dye)، نیلی رنگ (Indigo dye)، که برای پارچه های پنبه ای که بطور لایه ای آزاد نگه داشته شده، ساخته می شود. فرایند تولید پارچه دنیم و پارچه خاکستری تا مرحله رنگرزی در بخش آهارزنی شبیه است. پارچه دنیم در این مرحله رنگرزی می شود، اما در مورد پارچه خاکستری بسته به محصول نهایی در مورد رنگرزی آن تصمیم گیری می شود.
ریسندگی:
اولین مرحله ازپروسه تولید دنیم باز کردن و مخلوط کردن الیاف است. باز کردن با جدا کردن عدل های پنبه به تکه های کوچکتر شروع می شود. مخلوط الیاف پنبه در خط بازکننده الیاف صورت می پذیرد. این عدل ها با استفاده از داده های USDA High Volume Instrument (HVI) انتخاب می شوند و نرم افزار PCCA (نرم افزاری رایانه ای و انحصاری برای مخلوط کردن) استحکام بهینه نخ را تعیین می کند.
پنبه با مکش هوا از خطوط باز شدن و مخلوط شدن، از یک تمیز شونده اضافی و ماشین مخلوط کننده عبور کرده تا به ماشین کارد برسد. عمده عملکرد کاردینگ، حذف مواد خارجی و الیاف کوتاه، ایجاد یک وب از پنبه و تبدیل آن به یک فرم طنابی شکل است که به نام "فتیله" شناخته می شود.
پروسه کشش یک فتیله از 6 فتیله کوچک دیگر ایجاد می کند. مخلوط کردن اضافی، موازی کردن الیاف و تمیز کردن در این پروسه، فتیله مذکور را برای ریسندگی رینگ و یا چرخانه ای (Open End) آماده می کند. برای ریسندگی رینگ، فتیله بایستی یک مرحله اضافی را نیز طی کند که نیمچه نخ (Roving) نامیده می شود.
در ریسندگی چرخانه ای ، الیاف پنبه بواسطه یک عمل سانتریفیوژی به نخ تبدیل می شوند. الیاف مجزا درون یک روتور ریسندگی سریع چرخانده شده، تاب خورده و تبدیل به نخ می شود. سپس این نخ های تولید شده درون بسته های بزرگی جمع آوری می شوند.
الف) ریسندگی چرخانه ای (Open-End) :
در این ماشین ریسندگی ربات هایی در طرفین تعبیه شده اند که بصورت بخش بخش انتهای پاره شده نخها را به هم وصل می کند در یک مسیر متفاوت، ربات دیگری وجود دارد که بطور اتوماتیک عملیات رد کردن را انجام داده (خارج کردن بسته کامل/ عمل داف کردن بوبین) و پروسه نخ پیچی روی بوبین جدیدی را آغاز می کند. اندازه و کیفیت نخ روی هر بوبین توسط یک سیستم پروفایل بارکو (Barco Profile System) پایش می شود تا از یکنواختی اطمینان حاصل گردد.
ب) ریسندگی رینگ (Ring) :
در این ریسندگی،؛ فریم های ریسندگی، نیمچه نخ را با یک سیستم انتقال از ماشین نیمچه نخ می گیرند. نخ از الیاف پنبه تشکیل می شود که به یکدیگر تاب می خورند که بعد از عبور از بین سه غلتک استیل و سه غلتک رابری، برای تابیدن بدور همدیگر آماده می شوند. سپس نخ روی بوبین در حال چرخش روی اسپیندل (توسط تراولر) پیچیده می شود. رابطه بین سرعت غلتک، سرعت تراولر و سرعت اسپیندل توسط مقدار تاب نخ کنترل می شود. سطوح پایین انتهایی و اطلاعات تولید توسط سیستم تخصصی اوستر رینگ جمع آوری می شود. فریم های ریسندگی بطور اتوماتیک بوبین های نخ پر شده را خارج کرده و آنها را به بخش بسته بندی می فرستد.
ACG همچنین ظرفیت تولید نخ های چرخانه ای Amsler را داراست که با عنوان نخ تابیده شدهی حلقوی فاوکس شناخته می شود. این تکنولوژی ACG را قادر می سازد تا الگوهای نیم تاب مختلفی را درون یک نخ چرخانه ای پیاده کند. دنیم ساخته شده از این نوع نخ ها، ویژگی نخ و جذابیت سطحیای دارد که با نخ های چرخانه ای سنتی نمی توان به آن دست پیدا کرد.
بافندگی پارچه دنیم
الف) نخ خاکستری /خام تکمیل نشده روی بوبین های مخروطی شکل
بطور معمول نخ های مورد نیاز برای بافندگی از هر دو سیستم ریسندگی رینگ و چرخانه ای به فرم های مخروطی شکل دریافت می شود. برای بافندگی، نخ ها در دسته های زیر طبقه بندی می شوند:
· نخ تار
· نخ پود
عموما برای بافندگی، نخ تار باید در حد رضایت بخشی مستحکم باشد تا بتواند در برابر تنش ها و کشش های اعمالی در طی عملیات بافندگی مقاومت کند. به همین جهت، آنها دارای (Count Strength Product) یک معیار استحکام قدیمی(CSP)و اندازه بیشتری هستند تا استحکام آنها را افزایش دهد. نخ پود مستقیما در ماشین بافندگی استفاده می شود و در بعضی از موارد، اگر نیاز باشد، برای بهبود عملکردش در بافندگی، دوباره پیچیده می شود.
ب) چله پیچی بخشی / چله پیچی مستقیم:
نخ های تار نیاز است بصورت یک فرم صفحه مانند به ماشین بافندگی تغذیه شوند. در بافندگی، بوبین های مخروطی شکل بطور مجزا بر روی قفسه نخ قرار میگیرند (تعداد بوبین ها به ساختار پارچه بستگی دارد) و نخ از روی بوبین ها بصورت مجزا به درون فرم صفحه مانند کشیده و روی بیم / نورد تار پیچیده می شوند (برای بافندگی مستقیم) و برای چله پیچی بخشی بصورت بخش بخش بر روی دستگاه چله پیچی بخشی پیچیده می شوند. در واقع اگر صفحه نخ تار قرار است از رنگهای مختلف یا پترن های مختلف تشکیل شود تهیه نورد نخ تار با استفاده از دستگاه چله پیچی بخشی انجام می پذیرد.
ج) آهارزنی نخ در مجوعه/موقعیت نورد به نورد:
موضوع مد نظر در آهارزنی، بهبود استحکام نخ با بهم چساندن شیمیایی الیاف و همچنین بهبود ظرفیت مقاومت اصطکاکی با پوشش سطح نخ/الیاف است. بعلاوه، تعداد نخ ها در سطح چله در مقایسه با تعداد نخ های مورد نیاز در کل عرض پارچه خیلی کمتر است. از این رو، افزایش تعداد صفحات با کشیدن نخ ها از تعداد زیادی چله و مجدا ساختن یک صفحه جدید در ماشین آهار انجام می شود. در آهارزنی، بطور معمول بین 8 تا 12 درصد مواد آهار روی نخ تار قرار می گیرد. این بهبود در استحکام و مقاومت اصطکاکی نخ تار ضروری است، چون در طی بافندگی، نخ تحت تنش و کشش شدید و اعمال اصطکاکی خواهد بود.
د) نخ کشی:
بافندگی اساسا در هم تنیده شدن دو مجموعه نخ تار و پود در یک توالی و الگوی مورد نظر است. برای حصول این در هم تنیدگی، صفحه نخ تار به صورت دو لایه/صفحه تقسیم شده و نخ پود بین این دو صفحه وارد می شود. این عملیات تشکیل دهنه (Shedding) نامیده می شود. برای عملیات تشکیل دهنه نیاز است نخ تار از بین حفره های یک مجموعه از شافت های راهنما (میلمیلک ها) عبور کند. این عمیات نخ کشی(Drawing–in) نام دارد
ه) چله کشی یا گره زنی چله (Beam Gaiting):
نوردهای بافندگی نخ کشی شده، روی ماشین های بافندگی ثابت شده، نخ ها بسته و شافت های راهنما به هم متصل می شوند. این عملیات را چله کشی می گویند. اگر نخ های تار کشیده نشده بطور مستقیم به نخ های انتهایی چله وصل شود، عملیات گره زدن انجام شده است. این عملیات ضروری هستند چون چله های بافندگی بطور معمول تنها قادر به حمل طول مشخصی از صفحه نخ تار هستند و زمانی که بافندگی زیادی صورت پذیرد همه طول نخ موجود روی چله توسط ماشین بافندگی به پارچه تبدیل می شود. بعلاوه، طول نخ تار نیازمند تغذیه است که توسط دو عمل بالا می تواند انجام شود.
و) بافندگی:
همانگونه که پیش از این ذکر شد، بافندگی در هم تنیده شدن دو مجموعه نخ و ایجاد پارچه است. یک مجموعه نخ تار نامیده می شود که در فرم صفحه ای قرار دارد و دیگری نخ پود نامیده می شود که بین دو لایه از صفحه نخ تار به کمک حامل مناسبی مانند پروجکتایل، رپیر، جریان هوا، جریان آب وغیره انجام می شود. بنا به نوع ماشین بافندگی این حامل ها متفاوت هستند. انواع متفاوتی از فناوری برای ماشین های بافندگی در دسترس است که در ذیل به آنها اشاره شده:
· سیستم بافندگی ماکودار مرسوم با بافندگی معمولی یا اتوماتیک
· سیستم های بافندگی بدون ماکو با جت هوا، جت آب، رپیری، پروجکتایل
بافندگی ماکویی یک فناوری مرسوم با حجم تولید کمتر، سرعت پایین و فرسودگی بیش از حد ماشین آلات است. این فناوری امروزه منسوخ شده است. دنیم توسط این سیستم بافندگی به ندرت تولید می شود و بیشتر از سیستم بافندگی جت هوای کمپانی سوداکوما نوع 96 (ZAX-e) یا سیستم بافندگی رپیری و یا پروجکتایل استفاده می شود. این سیستم ها با شیوه پودگذاری قابل تمییز هستند که بطور خلاصه در ذیل به آنها اشاره شده است.
جت هوا: این سیستم یکی از اخرین پیشرفت ها در فناوری بافندگی است که در آن نخ پود به کمک فشار هوا پودگذاری می شود. سرعت بسیار بالای پودگذاری این سیستم (تا 1800 متر بر دقیقه) توسط این سیستم قابل دستیابی است. در مقایسه با رپیر و پروجکتایل، این سیستم تطبیق پذیری کمتری دارد اما اقتصادی است و در حجم وسیعی از واحد های تولید نساجی از جمله تولید دنیم کاربرد گسترده دارد.
تکمیل
الف) پارچه خاکستری / پارچه خام تکمیل نشده
پارچه بافته شده نهایی یا پارچه خاکستری، که عمدتا اینگونه نامیده می شود، روی غلتک پارچه پیچیده شده، از ماشین بافندگی در فواصل مشخصی خارج شده و به جهت امکان وجود خطاهای بافندگی بررسی می شود. اگر در حین بررسی خطاهایی در هر کجای پارچه مشاهده شود، مراحل اصلاحی مشخصی در بافندگی، چله کشی، آهارزنی و ... انجام می شود. بنابراین این خطا ها در محصولات بعدی می تواند به حداقل برسد. این یک عمل کنترل کیفی است.
ب) پارچه دنیم
این پارچه از 100 درصد پنبه بافته می شود و میتواند بسیار مستحکم و بادوام باشد. دنیم های آبی سنتی دارای طرح بافت 3 به یک (3 x 1 twill) بودند که نخ تار بطور جداگانه رنگ می شد و نخ پودبصورت رنگ نشده به کار برده می شد. ظاهر و کیفیت پارچه دنیم بعد از رنگرزی باید بهبود یابد، پروسه ای که روند آن از دستگاهی به دستگاه دیگر متفاوت است. بطور معمول، پروسه رنگزی تعیین کننده فناوری تولید دنیم است.
رنگرزی برای پارچه دنیم در مرحله آهارزنی انجام می شود. طور معمول، 2 شیوه پر استفاده برای رنگرزی پارچه دنیم وجود دارد:
· رنگرزی طنابی
· رنگرزی صفحه ای (عرض باز)
یک کمپانی می تواند هر یک از این شیوه ها را انتخاب کند. در کشورهایی مانند هندوستان رنگرزی عرض باز معمول تر است که دلیل آن مزیت هایی است که نسبت به شیوه رنگرزی طنابی دارد:
· نیازمند سرمایه کمتر
· ثابت شده بودن متد
· هزینه تولید کمتر
· زمان تولید کوتاه تر
· ساده تر بودن کار با ماشین ها
مشکل اصلی این شیوه رنگرزی وجود تنوع شید از مرکز به سمت لبه هاست.
ج) پروسه رنگرزی صفحه ای (عرض باز)
این پروسه چندین بخش از پروسه رنگرزی طنابی را حذف می کند. صفحه نخ با مواد شیمیایی مانند سود سوزآور شسته و بعد از فشرده شدن آب اضافی آن خارج می شود؛ سپس این نخ مجاز به یک بار عبور از حمام رنگرزی است تا اکسید شدن و گسترش رنگ روی نخ رقم بخورد. بعد از رنگرزی، نخ رنگ شده مجددا با آب تازه برای دو یا سه مرحله شسته شده و در نهایت قبل از ورود به بخش خشک کن ها، فشرده می شود. نخ رنگ شده به دستگاه آهار وارد و آهار زنی انجام می شود. بعد از آهار زدن، نخ تار آهار خورده به بخش بافندگی می رود. پس از بافندگی، پارچه دنیم بافته شده، برا انجام پروسه های تکمیلی مختلفی (مانند برس زنی، پرز سوزی، شستشو، خشک کردن و ...) به بخش تکمیل می رود. برس زنی و پرزسوزی باید ناخالصی ها را حذف و به یکنواختی سطح پارچه کمک کنند. سفتی و زیردست پارچه در هنگام آبرفتگی فشاری نیز تعیین کننده ثبات ابعاد پارچه است.
حتی امروزه هم پارچه های دنیم که با رنگی به جز رنگ نیلی (رنگ ایندیگو) رنگرزی می شوند، دنیم معتبری نامیده نمی شوند. در ابتدا زمانی که پارچه دنیم وارد بازار مد شد، تولید کننده های دنیم از رنگ های نیلی طبیعی (ایندیگوی طبیعی) استفاده می کردند که گران قیمت بود و یک پروسه تکمیل طبیعی را ضروری می کرد. اگرچه نیلی های مصنوعی (رنگ های ایندیگوی مصنوعی) به آرامی جایگزین نوع طبیعی این رنگ شدند، برخی از تولید کننده های سازمان نیافته هنوز از نوع طبیعی استفاده می کنند تا از جملهی تبلیغاتی " استفاده شده از رنگ های طبیعی" برندسازی کنند.
د) آماده سازی و بسته بندی کردن:
بافت پارچه در چندین اندازه یک عمل به صرفهی اقتصادی نیست، به همین جهت یک استاندارد عرض پارچه معمولا برای تولید فرستاده و پارچه ها در ماشین به میزان عرض مطلوب بریده می شوند. پارچه دنیم و پارچه خاکستری /خام بطور جامع بررسی می شوند تا نواقص زیر در صورت موجود بودن شناسایی شوند:
· نواقص بافت
· نایکنواختی رنگرزی
· عیب سفیدگری و رنگرزی
· لکه چربی
· وصله ها
در اینجا محصول نهایی از نظر کیفیت طبقه بندی می شود. سپس محصولات تایید شده تفکیک شده و به دپارتمان بسته بندی می روند در حالیکه محصولات معیوب، برای اصلاح ارسال می شوند. پس از بازرسی، بسته ها با پوشش پلی اتیلن بسته بندی و بنابر مشخصات خریدار، ارسال می شوند.